Problem:
Concrete & Steel corrosion, a common issue in building construction, can significantly impact the durability and safety of structures. Over time, environmental factors, moisture, and chemicals can cause corrosion of the steel rebar within the concrete, leading to structural deterioration.
With the advent of new, and innovative aggregate mixtures, the effects of corrosion can be even more extreme.
Elementale Enterprises offers an innovative solution to combat this problem through our Anti-Corrosion Treatment program. By applying this treatment to the rebar and concrete, we not only protect the structural integrity but strengthen to resist further damage, while also contributing to sustainability. Our treatment ensures the longevity of the concrete and, in turn, the entire structure, reducing the need for frequent repairs and replacements.
How:
There are two (2) major concrete problems, “Internal” and “On the Surface”.
Internally, corrosion is caused by metal in the rebar electrochemically reacting to the environment. This results in spalling concrete and ASR (Alkali Silica Reaction).
On the surface, corrosion is caused by embedded and surface mounted metal components on the floor that prevent proper moisture migration, which could lead to moisture damage and mold.
With moisture, oxygen, electrolytes (i.e. salts or acids), temperature changes and even galvanic reactions from material compatibility - corrosion over time to unprotected metal components causes rust. By the time rust is seen, corrosion is already present and damaging critical components (i.e. rebar, bolts, dowels, tie-rods, tendons, drainage grates, etc) that can lead to delamination and reduced structural performances.
The pH is an important indicator of the corrosivity of the electrolyte attached to a metal surface. The electrolyte and aggregate mixture combined with oxygen and moisture will impact the degree of corrosion on various alloys. For example, for carbon steel such as found in rebar, the corrosion rate is relatively low in aqueous solution, around a couple of thousandths of an inch per year, when the pH is between 3 and 9; however, below 3 it dramatically increases, and above 9 the corrosion rate decreases.
In the case of aluminum, the corrosion rate in aqueous solution will increase below 4 and above 8.5.
The actual corrosion rate on a metal will also depend on other factors, mainly the presence or absence of oxygen and contaminants such as chlorides, sulfides, other chemicals, and particulates.
Until today, the three (3) common methods used for protecting metal components from corrosion are Cathodic Protection, Metal Surface Finishing (like Galvanizing) and Coatings/barriers to isolate the metal component from the corrosive environment.
These methods are costly, and maintenance intensive.
In cathodic protection, this creates a costly installation requiring a sacrificial metal to be used to allow for the corrosion reaction. In many cases, these sacrificial metals are never replaced, giving a false sense of security while the metal becomes plagued with corrosion.
Using Metal Surface Finishing (i.e. Galvanizing, Anodizing, Electroplating) is also quite costly, works on some metals, not all. Ensuring proper adhesion and uniformity of the of the finished material to the rebar is a concern for long-term, due to complex geometries and irregularly shaped bars. Variation in thickness of the finishing material as well as compatibility to the concrete may result in localized corrosion. This may require the use of harmful toxins for the process.
Finally, traditional coatings have been adopted such as paints, epoxies and/or polyurethanes that are low-cost must be reapplied often due to their life-span. Their adhesion properties vary with temperature and humidity, which can affect their durability and longevity. Cure times can be long making the cost of labor and downtime for painting quite expensive. Handling rebar before coating is fully cured can lead to damage and/or premature failing of the coating creating problems in the concrete. Additionally, many of these products have high toxicity and VOC content, they are prone to UV and heat damage and will crack and peel.
A novel approach is a bio-degradable treatment that is absorbed INTO both the concrete and the metal. For the concrete phase, all salts are pulled out of the concrete and replaced by the propriety water-based gel to eliminate future pH concerns, while keeping the concrete porous.
For the metal phase, the Metal Corrosion Neutralization (MCN) treatment penetrates down to the surface of the metal, separates, and encapsulates the rust and neutralizes the metal for complete long-term protection of the surface area of the metal.
MCN Neutralizes the metal; continues to attract water to its surface – so no moisture hits the metal.
With the absorption characteristics, the MCN gets into any pits, is water-based, UL GreenGuard Gold certified and needs only basic pressure washing preparation on the metal instead of sandblasting and grinding.
Figure 1 shows how this treatment penetrates through the rust to the bare metal.
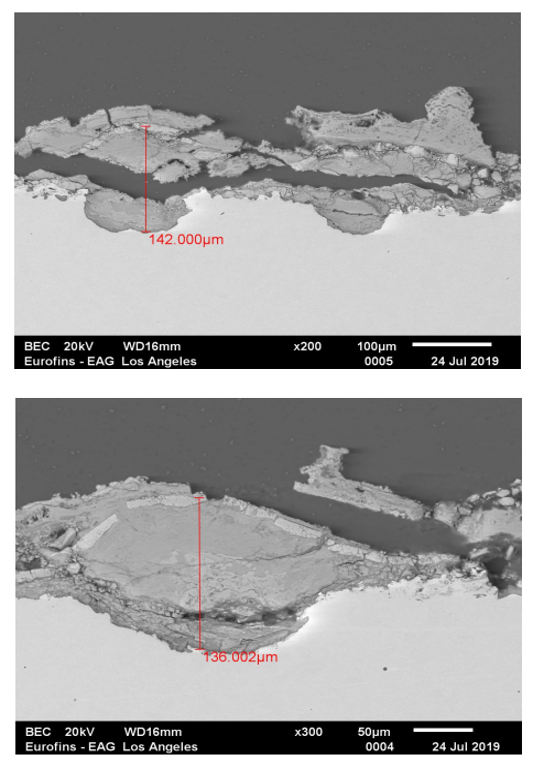
Figure 1: Dark Gray (MCN) has penetrated rust (gray) all the way to the white steel (white).
Penetration of Concrete
The Concrete Penetrating Solution migrates deep into the concrete (~6 inches) to pull out salts, chlorides, acids and even hydrocarbons and again neutralizes these components by bringing them to the surface for elimination.
Our studies have shown that up to 50% of the salts and chlorides are pulled out of the concrete!
Figure 3 shows the depth of penetration of the Concrete Permeation Solution that was sprayed onto the concrete in perpendicular passes after waiting for 40 hours. The penetration was observed under black light.
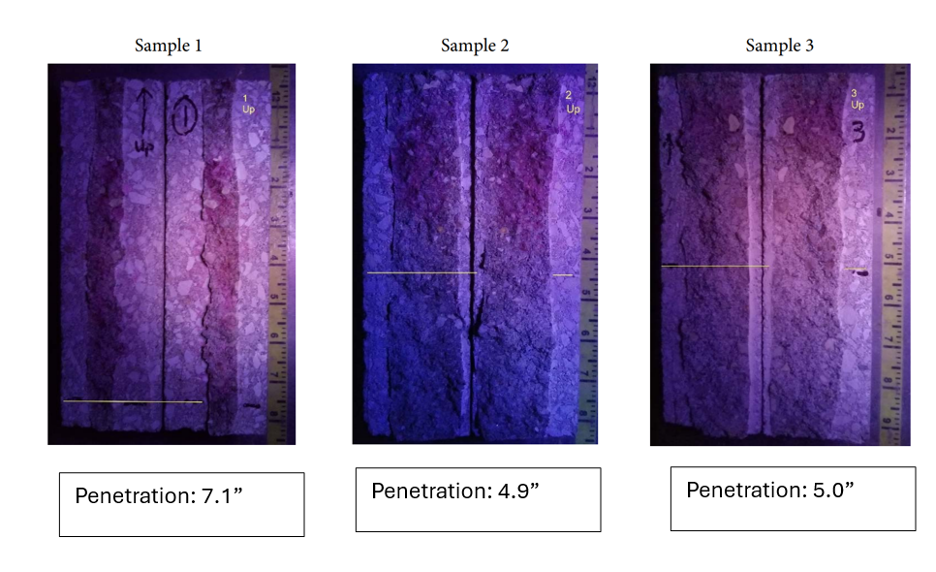
Figure 3: The average depth of Concrete penetration is 5.7 inches
The purging process may last up to two days and stops two major causes of corrosion and spalling – salts and chlorides.
Due to the porous nature of concrete, this revolutionary solution not only pulls out the salts, but also converts excess alkaline to a hydrogel that fills the empty pockets in the concrete, stopping future water from seeping through.
Must Meet the Rigorous Standards
1500 Hours – ASTM B117 – Salt Spray Test
Salt Spray Tests have been conducted showing no rust mitigation under the MCN treatment.
Left: Scribed panel shows bubbling and rust development in and around immediate area of scribe (V shape). No rust migration under the treatment, no peeling, treatment stays intact.
Right: Non-scribed panel with several pinholes cut into the center area. Taped edges allowed significant rust from uncoated edges to bleed through the tape. Coating shows no failure apart from slight bubbling and rust within areas where pinholes were cut.
No rust migration under MCN
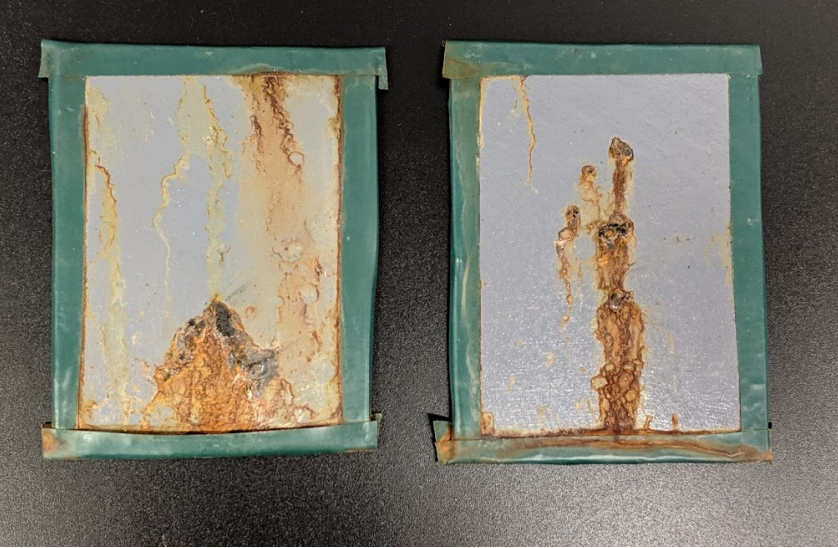
Figure 4: Treatment (gray) stays intact. Only scribed bits show signs of bubbles and rust at the point of damage.
NACE Pull Tests – Metal & Concrete
It is critical to understand the pull-off strength (commonly referred to as adhesion) of a coating system from metal substrates. This test offers two test protocols. Protocol 1 (test to fracture) determines the greatest perpendicular force (in tension) that a surface area can bear before a plug of material is detached.
The pass/fail criteria for typical coatings is 10-20MPa3. It is shown in Figure 5 that the pull test for the MCN exceeds1600 MPa and the C2M (Concrete to Metal) exceeds 1250 MPa. This is a true test of long-term strength and high impact durability.
NACE 232409 Pull-Off Strength (Adhesion Testing)
2.8 mils, 70 microns:
MCN (white)
• 10 Day Cure: 800 lbs/mm2
• 7 day Cure: 750 lbs /mm2
• 3 Day Cure: 400 lbs /mm2
C2M (gray)
• 10 Day Cure: 625 lbs/mm2
• 7 day Cure: 600 lbs /mm2
• 3 Day Cure: 400 lbs /mm2
Figure 5
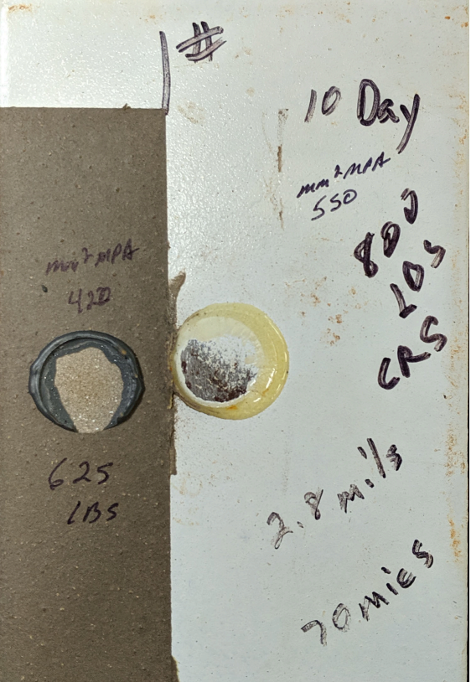
Figure 6 is an example of using this treatment routine on flooring with the need high impact strength. In this case, the High Impact topcoat was also used.
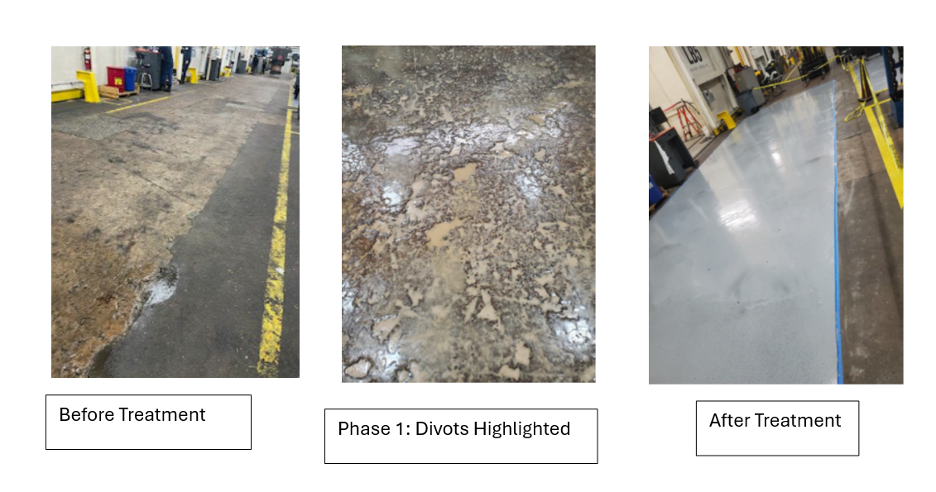
Figure 6: Concrete Permeating Solution was used on this hydrocarbon-laden floor, then High Impact Protection topcoat for additional protection against up to 50,000 lbs, while also keeping it water protected.
Concrete Penetration and Remediation
Working as a system on both metal and concrete, this treatment acts as a penetrant and barrier to solve widespread corrosion and erosion issues within concrete.
These products are designed to work and treat ongoing corrosion and damage by penetrating the concrete and metal, removing up to 50% of the salts and chlorides in the concrete and neutralizes the media to stop further cancer.
Since each step uses environmentally friendly products and penetrates deep within the media– they are easy to apply, quick cure times, safe for applicators as well as the environment – with a strength and longevity that far surpasses the natural lifetime of the concrete.
Figure 6 shows a typical treatment cycle that is quick and effective
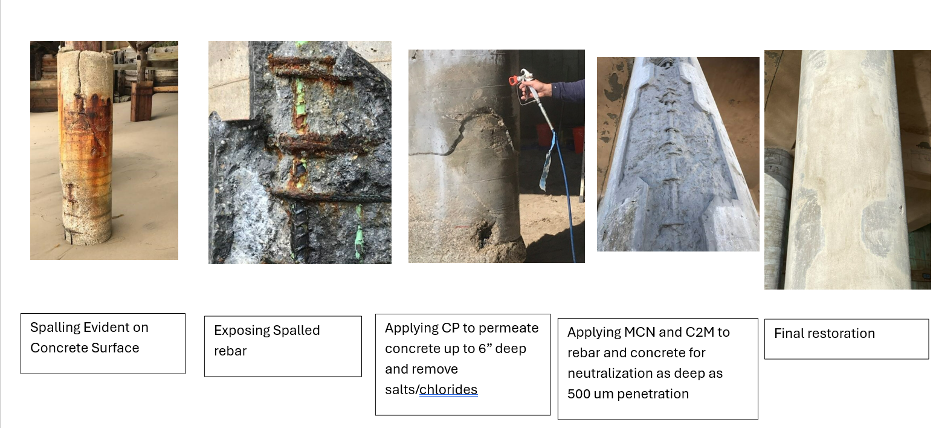
Summary:
Key Questions to Consider when selecting a rust inhibition program to prevent structural deterioration, maintain proper load bearing capacity, reduce frequent repair and replacement costs, while avoiding costly shutdowns and safety hazards.
• How critical is the presence of corrosion to the product quality?
• How critical is the need for proper water mitigation?
• How critical must the adhesion properties be between rebar and concrete?
• How Critical are seismic and other environmental conditions?
• How often are visual inspections being performed?
• How rapidly does the project need to be completed – to get back onto a production schedule?
• What is the frequency of salts, chlorides, sulfurs and other electrolytes to be in contact with the structure?
• What is the frequency of moisture being in contact with the structure?
• What are the thermal requirements on the product surface?
• What are your ESG goals?
By using an anti-corrosion treatment that penetrates both concrete and metal, environmental concerns are minimized, as MCN and CP block, neutralize and attract moisture for extreme long-term protection in any environment.
Addressing corrosion issues at early stages could reduce repair and replacement costs later, as well as reduce the risk of dangerous hazards and extremely expensive environmental release clean-up costs.
Footnotes:
1. NACE Standard SP0390-2009 (formerly RP0390), “Maintenance and Rehabilitation Considerations for Corrosion Control of Atmospherically Exposed Existing Steel-Reinfornced Concrete Structures” (Houston, TX: NACE International, 2009)
2. https://www.cement.org/docs/default-source/fc_concrete_technology/durability/is536-types-and-causes-of-concrete-deterioration.pdf?sfvrsn=4; 2016
3. Fletcher (Pull Off) Final (elcometerusa.com) , Society of Protective Coatings 2015
4. Allowable Stress Design of Concrete Masonry Columns - CMHA (masonryandhardscapes.org)